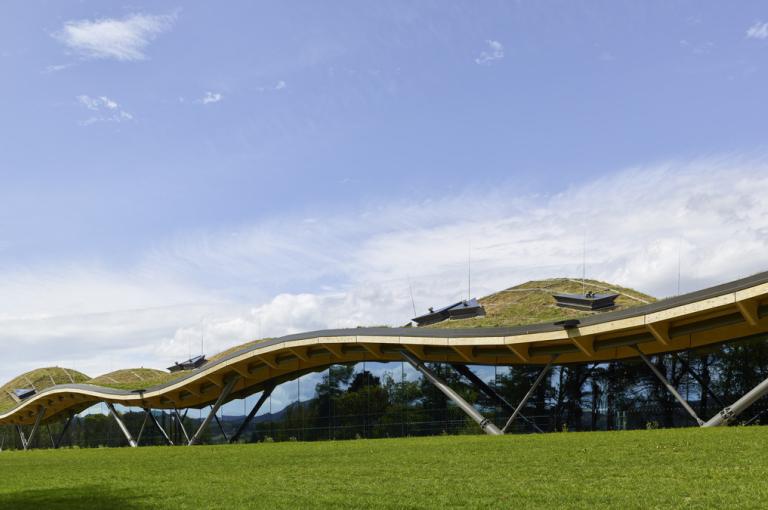
The Macallan distillery
Get in touch
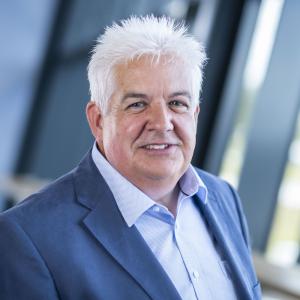
Summary
A cathedral to whisky
The £140m distillery was built on the stunning Easter Elchies estate in Speyside for Edrington, the international premium spirits company, with Robertson delivering the complex architectural design.
Robertson completed a flagship £140 million distillery and visitor experience for The Macallan, one of the world's leading luxury single malts.
Working with 25 contractors to bring the vision for the new distillery and visitor experience to life, Robertson took the complex and unique architectural design and moulded it to complement an area of outstanding natural beauty. This challenging build saw us apply all of our technical skills, innovation and expertise to create a seamless connection to the surrounding countryside.
During construction, up to 400 people specialising in more than 20 different trades were employed on site. Going forward, Robertson's facilities management business will provide maintenance services at the facility.
Natural materials – local stone, timber and the living meadow roof – as well as the landscaping design not only evoke the environment and ingredients of whisky production but also serve to provide an atmospheric journey for the visitor.
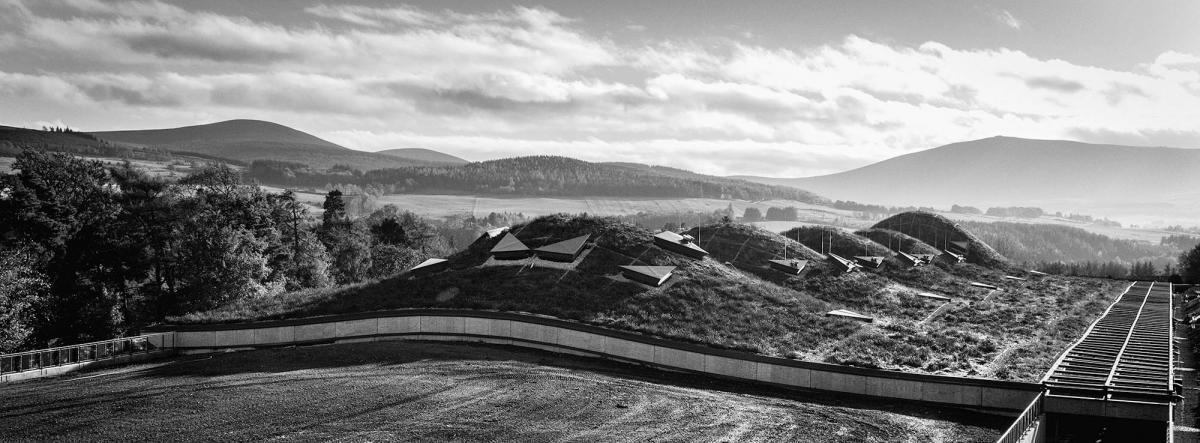
Creating The Macallan
At the outset of the project, 500,000 tonnes of earth was excavated. As the project was so close to the River Spey, a Site of Special Scientific Interest (SSSI), we worked closely with agencies to develop a bespoke water management system that would ensure zero environmental impact on the neighbouring watercourse. Infrastructure is vital, so we aligned access roads, both to deliver the project itself as well as to maintain 'business as usual' for The Macallan, while their new distillery was being built. We retained 100% of the excavated material on site, which required specialist lime stabilisation work. We also preserved the sands and gravels, which were screened and graded to be used as backfill and in the final landscaping. The result is a distillery that sits harmoniously within the surrounding countryside.
Roof structure
The roof comprises 1,750 glued laminated timber beams, making up a 3x3m grid that carries 2,500 cassettes that support the natural meadow roof covering. In total, there are over 380,000 individual roof components. It took almost 12 months of work, using collaborative design and bespoke parametric modelling software, to define the complex geometry, and realise the fluidity of the structure. The timber elements were manufactured in Austria using high-precision, computer-controlled technology, by Wiehag – one of the few companies in the world capable of this level of engineering. There were over 5,000 lifts, using 4 mobile cranes, to install the roof structure. In a similar way that timber barrels impart a flavour to whisky, the timber roof gives a unique character to this building.
Concrete
The project used 20,000m3 of concrete. Consistency and quality were key, so before any concrete was poured, a single concrete plant and raw materials were sourced for the entire project. A sampling facility was set up on site to adjust the use of admixtures, and closely monitor colour, quality of finish and performance. We demanded this level of certainty to ensure concrete could be poured from up to 12 m high, while still achieving the required detailing and high-quality finish. In particular, a 12 m high retaining wall, was critical to the process hall within the distillery, which sits underground within the landscape. This included some complex detailing, including 1m-wide circular columns and other sections which maintain a smooth, consistent curve.
Steelwork
The steelwork comprises 700 tonnes of beams supporting the distillery's unique roof. The architect's design was developed and manufactured by SH Structures, who are also known for The Kelpies in Falkirk. This process was software-driven and involved careful modelling and collaboration to ensure that the steel integrated correctly within the timber and the complex geometry of the roof. The beams are secured to the concrete frame at structural support nodes, where two circular hollow sections come together with a large division plate running through the middle and a baseplate at the bottom. The steel has been welded by specialist craftsmen who pride themselves on quality of detailing, meaning that the full structure remains a visible feature within the interior of the distillery.
The project was announced in 2012 and the build began in December 2014. The first whisky ran through the stills in December 2017 and the visitor experience will open its doors to the public on 2nd June 2018. Visitor numbers were expected to double in the first year and continue to rise thereafter.
An award-winning project
- Construction News 2019 - Project of the Year (over £50m)
- Royal Institution of Chartered Surveyors (RICS) Scotland awards 2019 - Design through Innovation award
- RIBA Stirling Prize 2019 shortlist for architects Rogers Stirk Harbour & Partners
- RIBA Scotland Regional Award 2019 and RIAS Award 2019 for architects Rogers Stirk Harbour & Partners
- Institute of Civil Engineers (ICE) Saltire Awards 2018 - Building of the Year
- Structural Timber Awards 2018 - Winner of Winners, Engineer of the Year and Highly Commended Project of the Year
- Wood Awards 2018 - Structural Award