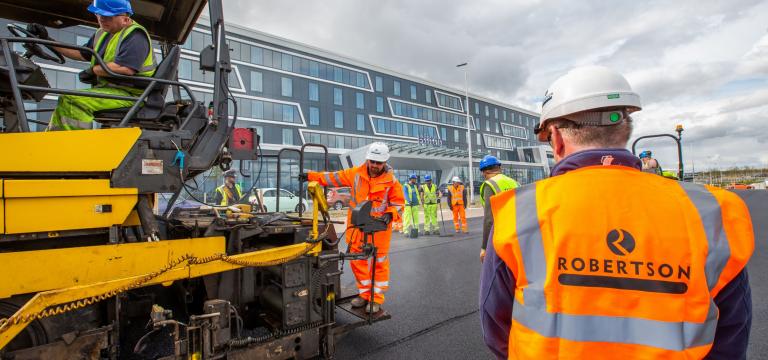
17 September 2019
Robertson lays plastic temporary parking area
Robertson lays plastic temporary area for parking at The Events Complex Aberdeen
Robertson has completed work at the newly opened The Events Complex Aberdeen to provide a temporary area for parking which has been made from asphalt containing three tonnes of waste plastic – the equivalent of 240,000 used plastic bottles.
- Engineers to use the equivalent of 240,000 plastic bottles to deliver project
- Three tonnes of waste plastic saved from landfill or incineration
- 4,600m2 of temporary road will be laid using waste plastic
Working in collaboration with Lockerbie-headquartered MacRebur, the team is to engineer a temporary area for vehicles to park near the Hilton Hotel within the TECA complex using three tonnes of waste plastic. The temporary area would only be used when the subterranean space at the venue cannot be used as a car park.
Kevin Gallacher, Managing Director for Robertson Civil Engineering said: "This is the first time waste plastic has been used to create a road in the city of Aberdeen. At Robertson we have a clear commitment to sustainability, and we are always looking for innovative ways to deliver for our clients. This new product takes a significant step to combat the effect of our harsh climate on road surfaces, but more importantly diverts reusable waste plastic from landfill.
"Working in collaboration with MacRebur, who developed the technology, the completed surface will cope better than traditional asphalt roads because it will withstand contraction and expansion caused by changes in the weather, which can create potholes and cracks and prove costly to repair."
The recycled plastic product will cover an area of 4,600m2. Traditionally, civil engineers would use asphalt made from a composite of bitumen and stone. However, with the introduction of this technology it means part of the composition is replaced with waste plastic.
It works by turning the waste plastic back to its original oil-based state, therefore reducing the need for fossil fuels and cutting carbon emissions as a result – saving 2.5 tonnes of carbon on this project compared to traditional surfacing.
Toby McCartney, CEO of MacRebur, said: "We're delighted that our product is being used at this high-profile development. This demonstrates Robertson's commitment to making choices in construction which help to protect the environment, setting an example in the industry."
The waste plastic is a carefully selected mix that is turned into granules and then melted and blended with stone to make asphalt. The final product does not look recognisably different, but because it contains plastic, is more flexible.
MacRebur only use plastic that melts at the temperatures used to make asphalt so that it homogenises fully without creating microplastics – like mixing sugar into a hot cup of tea.
The MacRebur waste plastic-enhanced asphalt was supplied and laid for this project by Leiths.