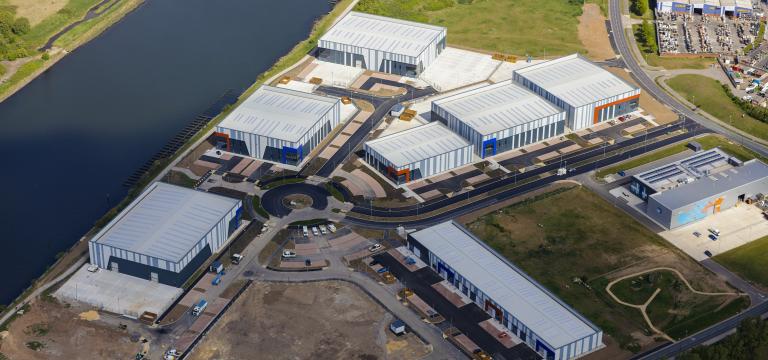
11 September 2020
Robertson diverts 99.99% from landfill upon completion of TeesAMP
Robertson diverts 99.99% from landfill upon completion of TeesAMP
Robertson Construction North East delivered on programme and to budget whilst utilising sustainable techniques.
Robertson Construction North East has completed works at TeesAMP in Middlesbrough and has delivered on programme and to budget whilst utilising sustainable techniques which saw less than 1 tonne of excavated material sent to landfill.
Heralded as a significant stride in addressing the national shortage of high-quality buildings suitable for modern advanced manufacturing companies and processes, TeesAMP spans 11 hectares and comprises of 14 modern offices across 8 units.
Under a design and build contract, Robertson was able to provide the best solution for the site on the former Newport Iron Works. Faced with ground that included iron ore slag which ran up to 10m in depth in some areas, the company excavated over 40,000m³ which was then reused to form foundations, capping for roads and to build up slab levels; 25,000m³ of the iron ore slag was crushed and reused throughout different parts of the site.
Dynamic compaction was utilised for the foundations of 5 of the units and 3 have Controlled Modulus column piling.
Garry Hope, regional managing director, Robertson North East, commented: "Dynamic compaction on the site provided a cost-effective solution which enabled us to utilise the existing ground and build it up. The Newport Iron Works are an important part of Middlesbrough's heritage and being able to use the iron ore slag throughout the project has meant that the site retains some of its history.
"One of the key design elements was the retention of the cycle path, which runs through the site, and is part of the Land Ends to John O'Groats route. We were able to use some of the crushed iron ore on the cycle path which gives this part of the route additional meaning as cyclists passing through connect directly with the proud heritage of the area."
In addition to reusing the materials available on site, Robertson procured the steel for the buildings from a local company. With sustainability high on the agenda, seven of the units are built in the same grid sections which resulted in economies on steel sheeting, resulting in zero waste and the ability for 3 of the units to be joined together should there be an occupier requirement.
With a number of key tenants already lined up, TeesAMP is set to be a blueprint for similar regeneration projects on brownfield sites.
Geoff Hogg,â¯chief executive,â¯Chaloner Group, the developer of TeesAMP, said: "Robertson Construction brought solutions to the project, which were of benefit both environmentally and financially. â¯This is an important site for the future of Middlesbrough and the wider Tees Valley and will be pivotal in the economic recovery and growth of the area as we attract new tenants that, in turn, will create valuable and sustainable new employment opportunities."
During the 65-week programme, Robertson also delivered employment and training opportunities within the local community, including work experience for 33 students from Middlesbrough College and the creation of 12 jobs through its sub-contractors.
Using BRE's SmartWaste environmental site monitoring and reporting software, Robertson was able to account for every material the team touched on site.
Garry concluded: "It's imperative that as an industry we are aware of our impact on the environment. TeesAMP is an excellent example of recycling and repurposing the resources available on site, and we are extremely proud that from a site spanning 11 hectares, our material sent to land fill could fit in a single bulk bag."